Innovations
Our engineers don’t stop until the job is done. Every Unibloc Hygienic Technologies pump is built with innovation that simplifies the pumping process and ensures product safety. We examined the unique needs of our customers across industries to develop technology like QuickStrip, SimpleSet and more that set us apart from the competition.
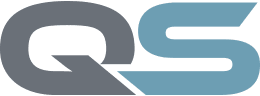
The Unibloc patented QuickStrip technology is designed to better handle the challenges of daily sanitation. Much of the damage sustained by pump components occurs during the sanitation process, resulting in expensive repair and re-machining. Our QuickStrip rotors and wear pads withstand wear and tear by providing plastic on metal contact, not metal on metal. They also offer tool-free disassembly, resulting in decreased downtime, an easier to maintain pump and lower cost of ownership.
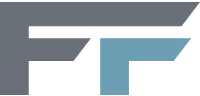
The Unibloc QuickStrip FoodFirst 600 pump is specifically designed to address the top concerns of our food processing customers – foreign material and pump damage. With fewer parts, one-way assembly, and several new safety features, it’s less susceptible to damage during cleaning, reducing the risk of foreign material entering the process stream.
AODD+ is the air-operated double-diaphragm pump like you’ve never seen before. While traditional AODD pumps have been on the market for many years, the Flotronic® One-Nut® technology creates an entirely new AODD solution that sets new benchmarks for durability, cleaning, and ease of use.
Its advanced design provides a higher level of performance, even in the most demanding applications.
As a world-leading manufacturer of air-operated double diaphragm pumps, the One-Nut design behind Flotronic AODDs revolutionized how diaphragm pumps can be used – including highly viscous food, beverage, cosmetic, personal care, and pharmaceutical applications. It’s become indispensable wherever hygienic applications and high productivity performance are critical.
The difference is tied to the One-Nut concept. This innovative technology boasts a streamlined, user-friendly design that simplifies maintenance and operation, ensuring maximum uptime and minimum downtime. Join the revolution of hundreds of facilities that took their performance to the next level with AODD+.
Traditional AODD vs Flotronic AODD+
You may have tried an AODD before. But that’s nothing like a Flotronic AODD+
Many industries demand that process equipment be fully drained and cleaned in situ. Flotronic’s unique One-Nut design enables it to be fully cleaned, using up to 7 Bar pressure from an external CIP pump, without the need to bypass the pump at all. Furthermore, there is 60% less product remaining in the pump needing to be cleaned than with any traditional AODD pump. This means less product is wasted, and quick cost saving CIP cycles are possible. The AODD+ can also be fully drained at the end of any CIP cycle without any manual intervention.
This allows in-line inspection/replacement of diaphragms in less than 15 minutes. The One-Nut enables a fast maintenance, fast strip down concept that turns the conventional pump’s daily maintenance routine inside out.
A Flotronic AODD+ payback is far faster than a traditional AODD!
Discover how quickly you can recover your costs—use our AODD Maintenance Payback Calculator to see your return in just a few clicks!
You may have tried an AODD. But that’s nothing like a Flotronic AODD+.
Explore Flotronic AODD+ Products
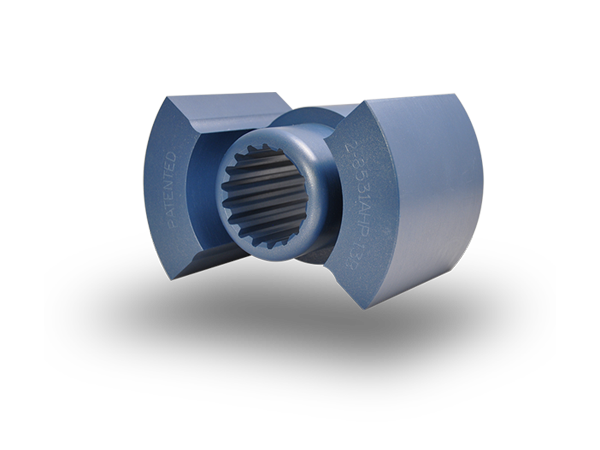
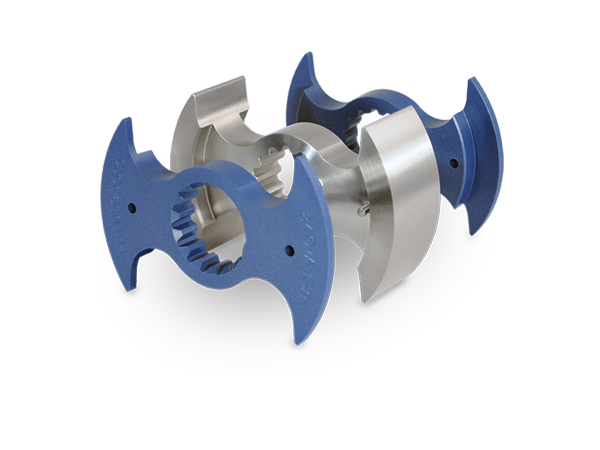
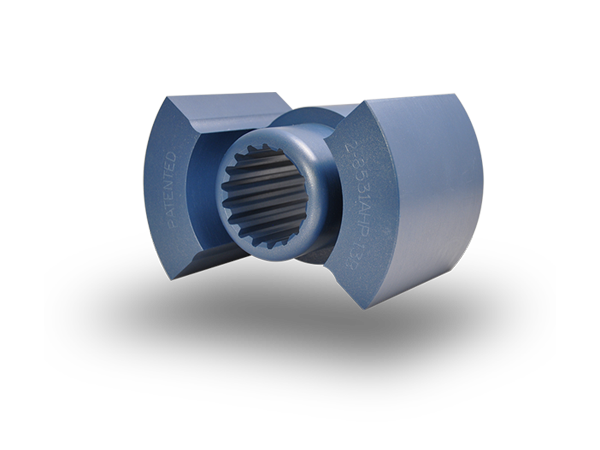
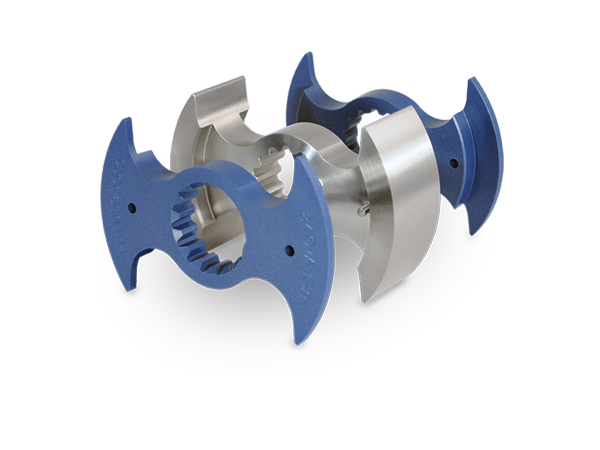
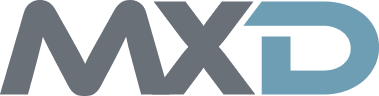
Building on our proven QuickStrip technology, QuickStrip MXD offers metal and X-ray detectability, ensuring product and production safety for the most demanding applications. We offer patented DuraCore MXD rotors and PolyFlex MXD rotors to choose from to suit any facility’s needs and budget.
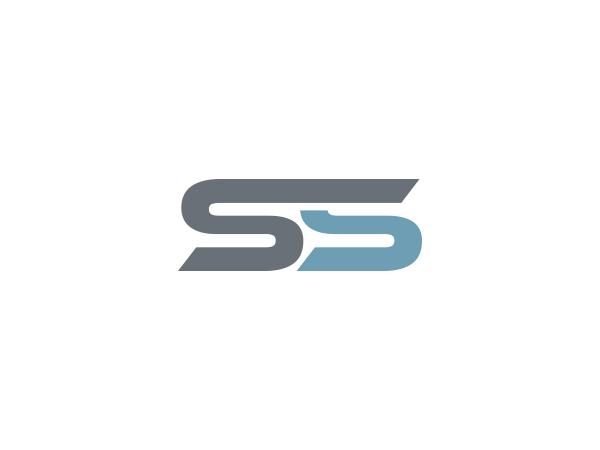
Unibloc pressure relief valves are outfitted with our SimpleSet technology. SimpleSet allows for a fully adjustable pressure range from 5-200 psi.
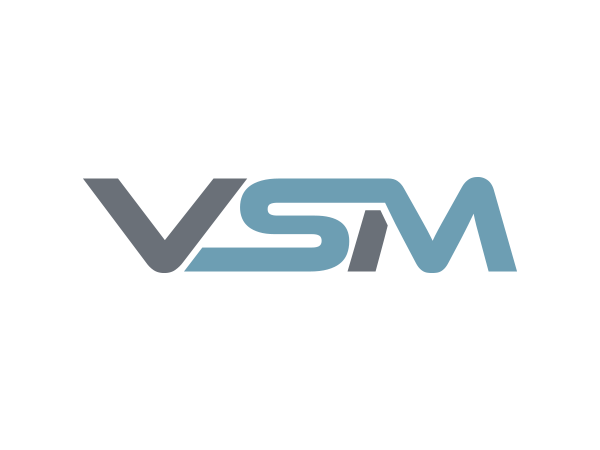
Our Versatile Seal Mounting (VSM) technology allows any Unibloc seal to easily mount on any pump head with no modifications. VSM is one of several ways we allow our customers to customize their pumps, even for applications requiring different seal types, to simplify their operations.

Processing managers and tanker fleet operators depend on hygienic lobe pumps. When they need service, or when they fail, downtime and replacement costs wreak havoc with operations budgets. Unibloc® CleanPlus™ lobe pumps address maintenance issues with innovative design features found only on a Unibloc pump. These features slash routine maintenance time, eliminate common damage points, and enhance product hygiene.
The heart of any lobe pump is its rotor, and unfortunately, it is also a potential cause of maintenance issues. Our bolt-free rotor design prevents damage caused by improper torquing. This eliminates crushed sleeves, deflected shafts, and catastrophic failures that plague pumps with conventional rotors. What’s more, each rotor and pump housing is milled from a single billet of stainless-steel, avoiding seams or weld transitions where bacteria or product could hide.
For pharmaceutical, cosmetic, and personal-care product applications where cleanliness is critical, CleanPlus pumps feature all-stainless-steel rotors that eliminate the risk of plastic wearing into your process. Unibloc pumps also include our patented FlushCap bearing that stabilizes the rotors while ensuring full Clean-in-Place (CIP) compatibility, maintaining the highest standards of sanitary performance.
When manual cleaning is necessary for highly viscous products, our proprietary QuickStrip® design transforms the maintenance process. Disassembly requires no tools and can be completed in minutes rather than hours–cutting pump cleaning times from two hours to just 20 minutes. This frees up valuable technician time and reduces downtime. In addition, the pump is designed for one-way reassembly, so it’s impossible for new maintenance technicians to cause damage due to improper reassembly.
The simplified pump design also means fewer spare parts to stock and less time spent training maintenance crews.
Join thousands of processors and fleet operators who have discovered how Unibloc CleanPlus pumps lower the total cost of ownership. When it comes to protecting your process and your bottom line, every minute – and every drop – counts.
Frequently Asked Questions
A hygienic pump is designed for applications where product cleanliness is vital, such as food, beverages, personal care products, and pharmaceuticals. Hygienic lobe pumps feature high-quality materials (typically 316L stainless-steel), smooth surfaces without dead spaces, and easy cleaning capabilities. To ensure food safety and product purity, hygienic pumps are compatible with standards from organizations like 3A and FDA.
Unlike other hygienic lobe pumps, Unibloc® QuickStrip® CleanPlus™ Pumps use rotors and housing milled from a single billet of stainless-steel, avoiding weld transitions that could harbor bacteria.
Lobe pumps are typically cleaned using CIP (Clean-in-Place) or SIP (Sterilize-in-Place) methods. With Clean-in-Place pumps, cleaning solutions are circulated through the pump at high temperatures. For more thorough cleaning, and when the product is too viscous for effective CIP, pumps can be partially disassembled (COP) to access all surfaces. Hygienic lobe pumps are designed with smooth, crevice-free surfaces to ensure effective cleaning and prevent bacterial growth.
Unibloc® CleanPlus™ Pumps can be cleaned in place or out of place. Unlike other Clean-in-Place pumps, they feature the unique QuickStrip® design. Workers can disassemble, clean, and return them to service in minutes rather than hours. The labor savings contribute to industry-leading low total cost of ownership.
CIP (Clean-in-Place) is a method for cleaning pumps without disassembly. It involves circulating cleaning solutions through the pump and connected piping at specified temperatures and flow rates. This automated process saves time and ensures consistent sanitization. Clean-in-Place pumps feature smooth surfaces and no dead spaces where the cleaning solution may not penetrate at an adequate rate of flow. When the application allows it, CIP is usually preferred because it allows cleaning without the need for a worker to strip down the pump.
The Unibloc® CleanPlus™ Pump is the only Clean-in-Place pump that uses bolt-free rotors. This design avoids the risk that workers improperly torque rotor bolts, leading to pump damage. To accomplish this, our pump uses a patented FlushCap bearing that stabilizes the rotor while still providing access to cleaning solutions. The end result is a more reliable, lower-cost-to-own pump.
The pharmaceutical pumps used in pharmaceutical and biotech processing are of several hygienic pump types: positive displacement pumps for viscous fluids, peristaltic pumps for precise dosing, and centrifugal pumps for high-volume transfer. Pharmaceutical pumps feature pharmaceutical-grade materials, electropolished surfaces, and sanitary connections. They are designed for CIP/SIP compatibility to maintain the sterile environments essential for pharmaceutical production.
The Unibloc® CleanPlus™ Pump meets all the requirements for pharmaceutical applications. Unlike centrifugal pumps, it handles shear-sensitive products gently.
Hygienic positive displacement pumps are divided into two main categories: rotary and reciprocating. Rotary pumps (including gear, lobe, and twin screw types) use rotating elements to move fluid through the pump chamber. Reciprocating pumps (including piston, plunger, and diaphragm types) use oscillating or back-and-forth motion to displace fluid. Both types of hygienic positive displacement pumps deliver consistent flow rates regardless of discharge pressure and are ideal for handling viscous fluids or applications requiring precise dosing. Unibloc® Hygienic Technologies is the only pump manufacturer that offers all four primary pump types for hygienic applications: gear, lobe, twin screw, and air-operated double-diaphragm pumps.